FlexSim超凡三维仿真平台赋能企业智慧升级新纪元
adminc2025-03-24单机游戏14 浏览
当效率与成本难以兼得,企业如何破局?
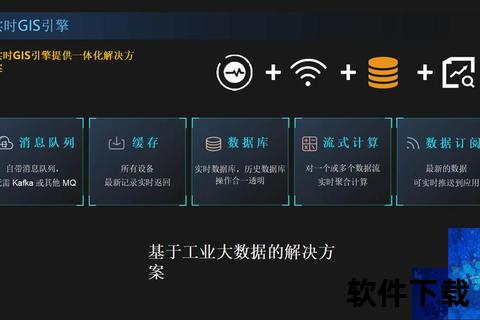
在制造业与物流业中,"拍脑袋决策"导致的资源浪费屡见不鲜:某电子厂因产线设计失误导致设备闲置率超40%,某物流中心因动线规划不当每年多支出300万运输费。传统试错式改进犹如盲人摸象,而FlexSim超凡三维仿真平台赋能企业智慧升级新纪元的核心价值,正是通过数字孪生技术将决策失误消弭于虚拟空间。
1. 生产流程优化能否突破经验桎梏?
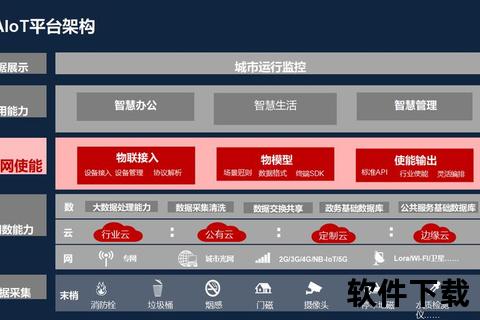
东莞某精密零件厂曾面临合格率不足65%的困境。通过FlexSim搭建的虚拟车间,工程师发现原正态分布加工参数存在系统性偏差——当处理器均值设为12秒时,实际合格率因标准差波动大幅降低。平台特有的标签系统精确记录每个工件的entry_time与finish_time,最终将加工时间标准差优化至0.8秒,良品率提升至89%。
更值得关注的是其动态响应能力。某汽车零部件厂利用平台的正投影图形编辑器,仅用3天就重构出包含12道工序的数字产线。当模拟订单量突增20%时,系统自动触发暂存区容量预警,指导企业提前调配AGV运输资源,避免现实场景中的产线堵塞。
2. 仓储系统如何实现"零库存"愿景?
深圳某3C产品仓储中心的案例颇具代表性。该中心原采用人工分拣,高峰期错发率高达7%。通过FlexSim的流结点与交通控制实体建模,工程师发现错发主要源于分拣路径交叉。平台创新的网络节点功能,最终规划出双向智能分拣轨道,使AGV空驶率从38%降至12%,分拣准确率达到99.97%。
在浙江某医药冷库项目中,工程师利用平台的时间表功能模拟极端天气下的设备运行。当模拟环境温度骤降至-25℃时,系统精准预测出制冷机组MTBF(平均无故障时间)缩短27%,指导企业提前部署冗余设备,避免价值千万的药品损毁。
3. 产线协同怎样跨越"数据孤岛"?
重庆某摩托车制造厂的转型堪称典范。该厂原有8条独立产线,物料协同效率不足60%。通过FlexSim超凡三维仿真平台赋能企业智慧升级新纪元,工程师创建了包含68台设备、23个工序节点的数字孪生系统。平台特有的任务执行器功能,使焊接机器人等待时间从平均47秒缩短至9秒,整体设备利用率突破85%。
更突破性的应用出现在某新能源电池厂。借助平台的Excel数据导入功能,企业将过去三年12万条生产数据注入仿真模型。当模拟新增21700型圆柱电池产线时,系统自动匹配历史最优参数组合,使新产线调试周期从常规的45天压缩至11天。
数字孪生时代的生存法则
FlexSim创造的虚拟试验场已帮助超过200家企业实现降本增效,但技术落地需遵循三大原则:首先建立"模型-现实"数据闭环,建议每周同步实际运营数据;其次设置动态预警阈值,当模拟偏差率超5%时启动模型校准;最后构建决策沙盘,重大投资前需通过3种以上情景模拟。正如某车企生产总监所言:"现在任何设备采购合同都必须附带仿真验证报告,这是避免千万级失误的数字化保险。
FlexSim超凡三维仿真平台赋能企业智慧升级新纪元的真正价值,不仅在于规避风险,更在于创造传统思维难以企及的可能性——当某物流企业用平台模拟出"无人机+AGV"混合配送方案时,他们发现夜间配送成本可比纯人工模式降低41%。这启示我们:在虚实交融的新纪元,敢想敢试的数字勇气,才是企业突围的关键。